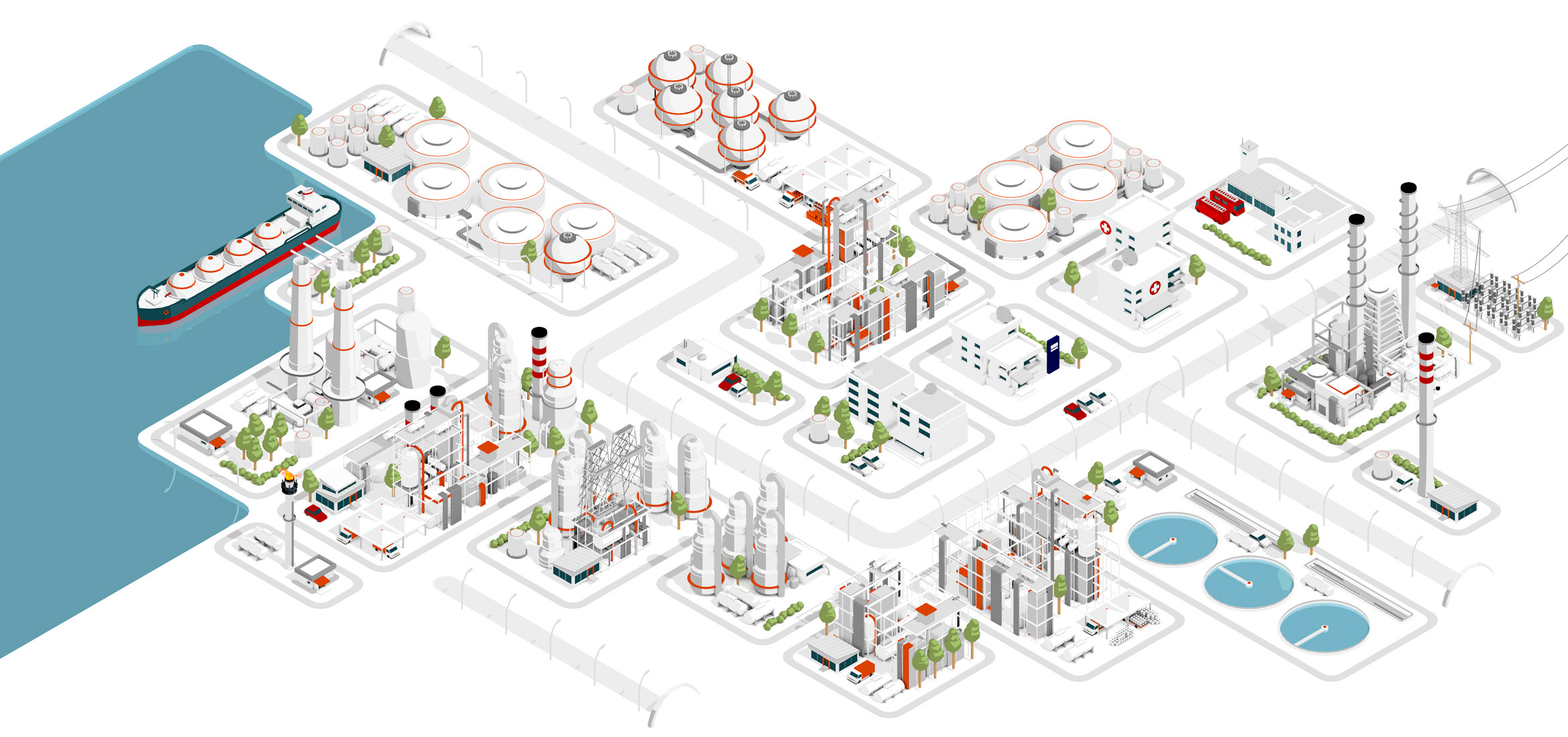
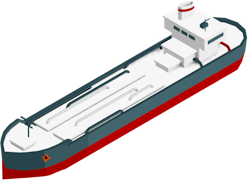




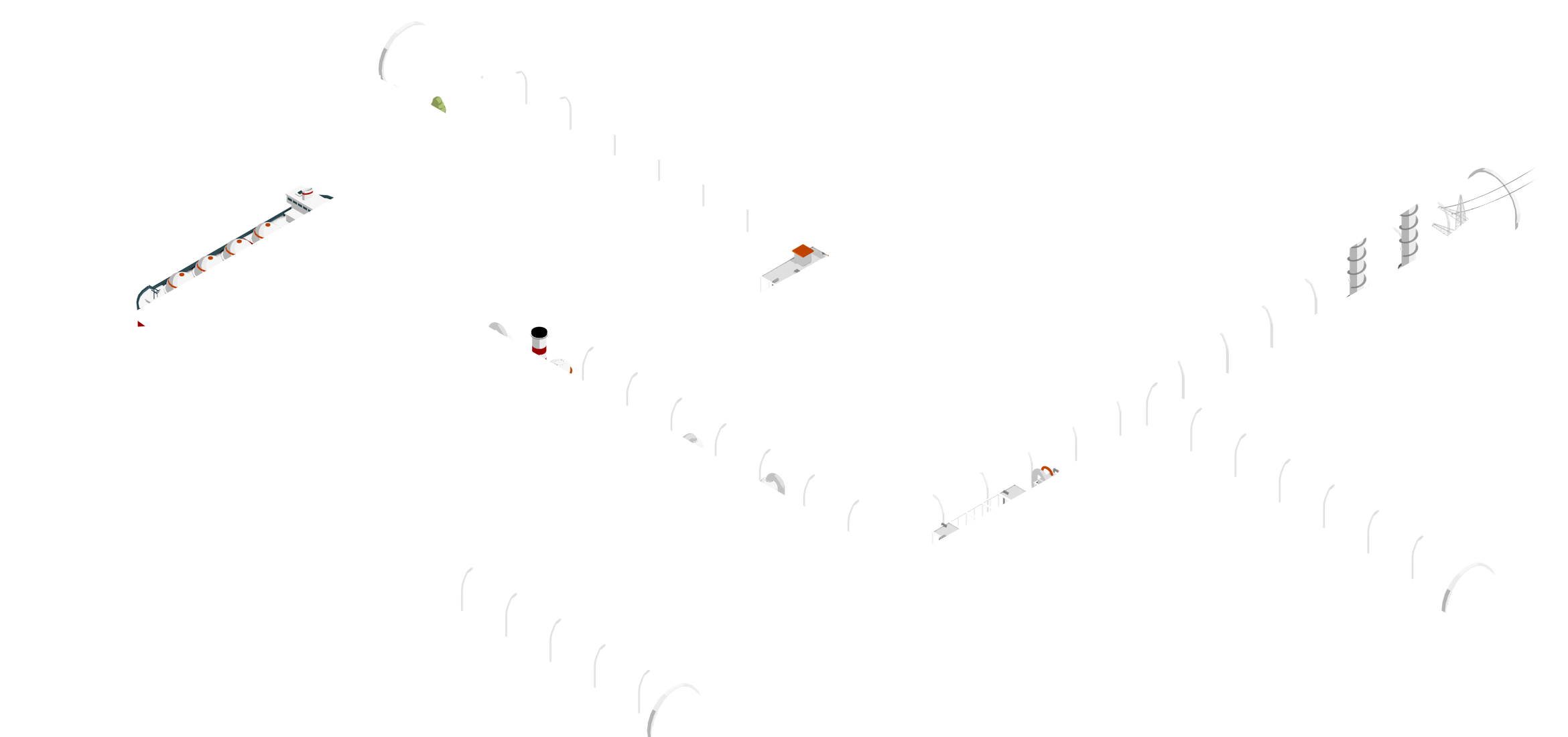
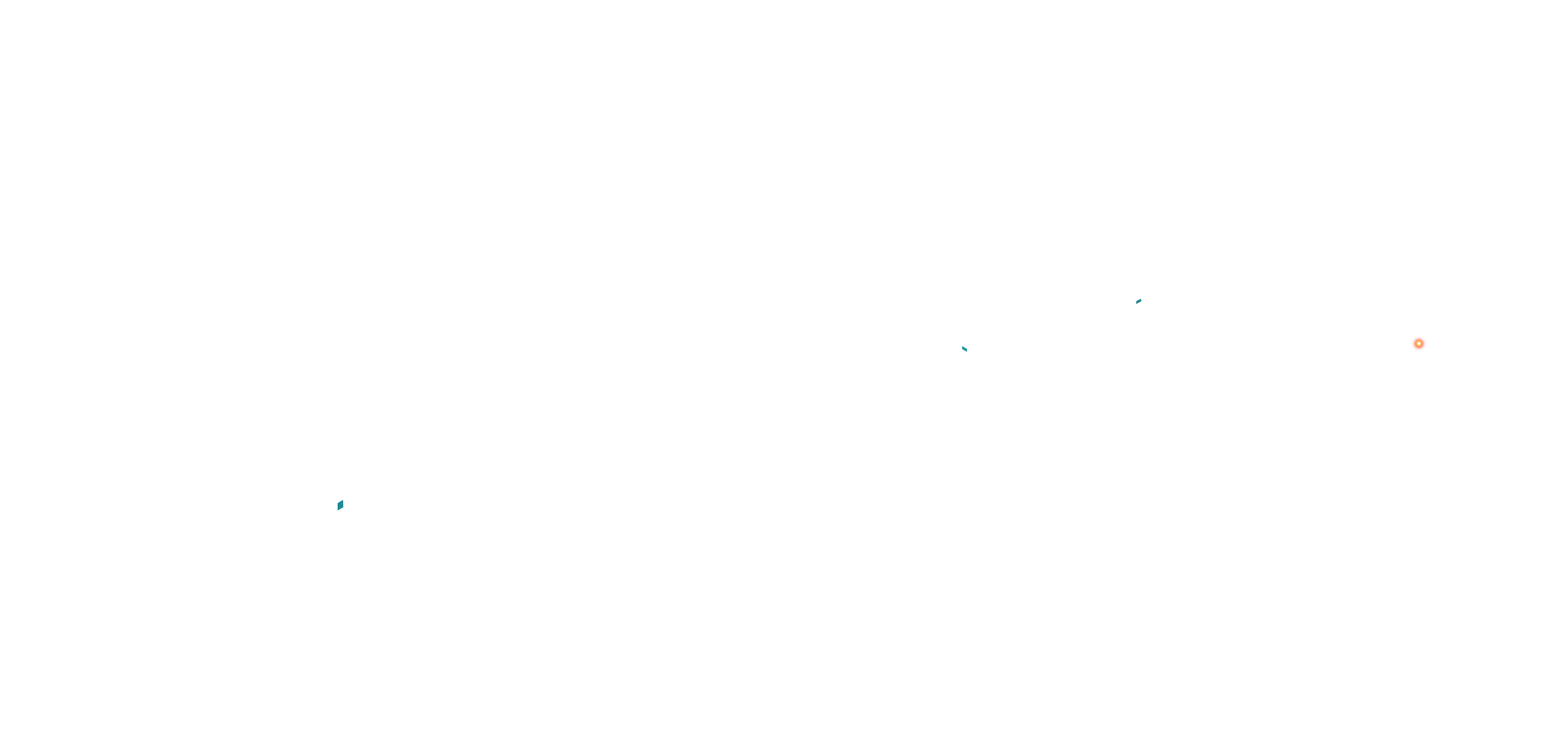
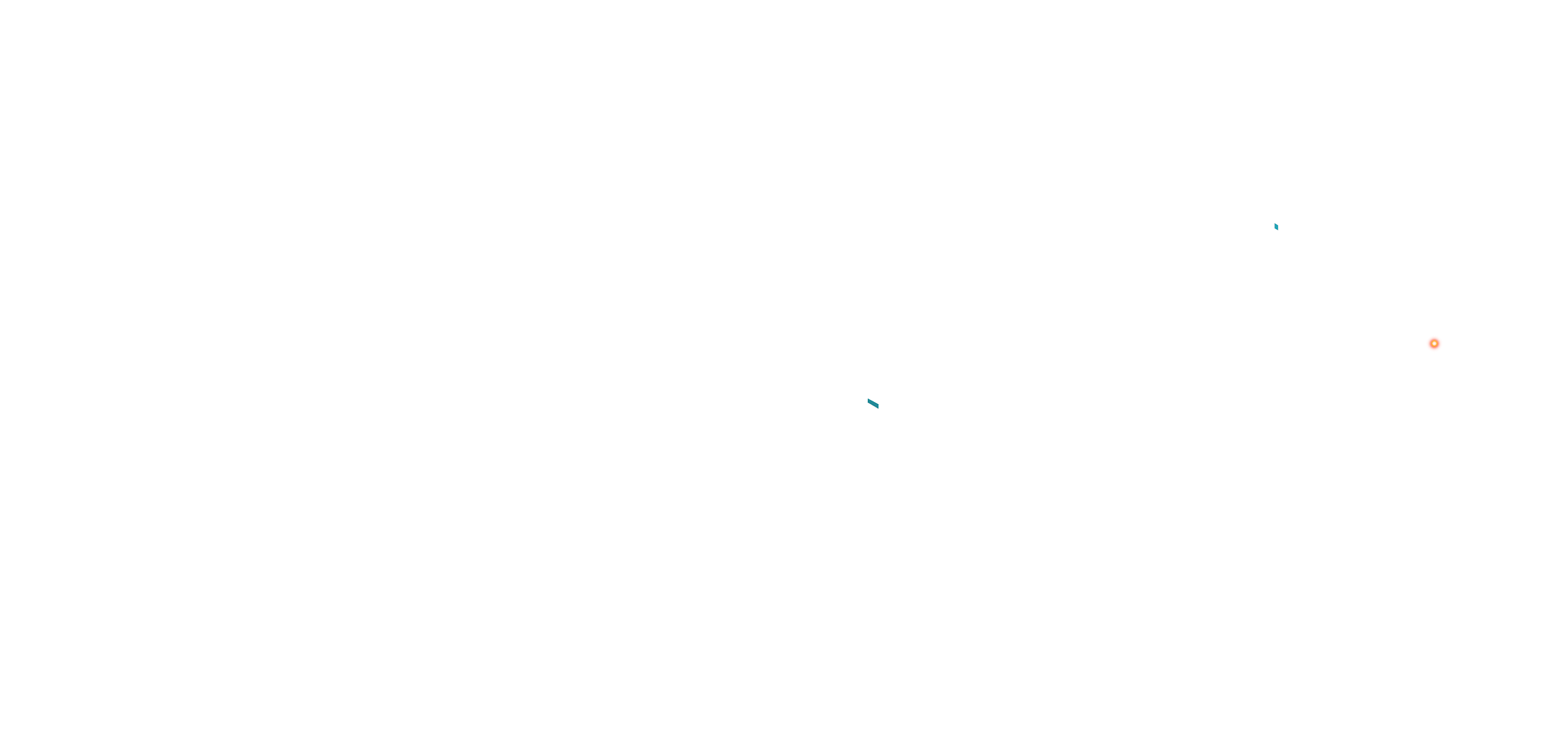
Nuestras instalaciones
En el Complejo Industrial de Cartagena fabricamos numerosos productos de uso diario en nuestra sociedad. El gas butano o propano que dan calor al hogar, los combustibles que hacen funcionar millones de vehículos y muchos más.
Más información
El terminal marítimo es el lugar al que llegan los petroleros cargados de crudo y desde el que enviamos algunos productos ya refinados para su comercialización. El puerto recibe petroleros de hasta 315.000 toneladas procedentes de cualquier parte del mundo.
Hemos construido cinco muelles nuevos para evitar que los barcos tengan que esperar a que haya un lugar libre y aumentar así la seguridad. Una vez atracados, el crudo de sus tanques se traslada a través de tuberías hasta los depósitos situados en tierra del área de logística y almacenamiento.
La capacidad total del complejo es de tres millones de metros cúbicos, que equivalen a 1200 piscinas olímpicas.
Desde el cuarto de control se analiza todo el crudo y se supervisa el proceso. Allí se mide la cantidad de petróleo que fluye por las tuberías, asegurando las operaciones y descartando cualquier riesgo.
Las tuberías que recorren todo el complejo son de diferentes colores según el producto que transportan: las rojas, aguas contra incendios; las amarillas, gas; y las verdes, agua de proceso. Las grises por su parte, son las encargadas de llevar el producto hasta los tanques repartidos por todo el complejo. Cada uno de ellos está preparado para conservar el crudo en las mejores condiciones.
En los tanques se elimina el agua que pudiera contener el crudo y se mantiene la temperatura para controlar la viscosidad del petróleo: a mayor temperatura, menor viscosidad. Su control se realiza mediante calefactores o serpentinas ubicados en la parte inferior del tanque. Para no perder hidrocarburos volátiles poseen techos flotantes que evitan este tipo de fugas.
CORES (Corporación de Reservas Estratégicas de Productos Petrolíferos) también almacena 1,6 millones de metros cúbicos de productos petrolíferos en las instalaciones de Cartagena. Son reservas de crudo estratégicas, un stock de producto listo para ser utilizado en caso de que España se quedase sin suministro de petróleo del exterior. Con esa cantidad España sería autosuficiente, al menos, durante cuatro meses.
Además de tanques de crudo, existen otros que almacenan el producto resultante después del proceso de refino. En la zona donde se almacenan productos terminados, existe una capacidad superior a 1,5 millones de metros cúbicos. Desde estos tanques, el producto se distribuye por toda España a través de la red logística de CLH.
Una vez eliminadas las impurezas, el crudo se trata con calor en lo que se conoce como destilación atmosférica. Se lleva a cabo en torres que permiten separar sus componentes tomando como base la diferencia de volatilidad. Así se extrae fuelgas, gas licuado de petróleo (GLP), naftas y destilados medios (gasolina y queroseno).
El fuelgas, al que se le extrae el azufre, se utiliza para dar energía eléctrica al complejo a través de las plantas de cogeneración. Las naftas pasan por un proceso de reformado para convertirse en gasolinas y en GLP para coches que se mueven con autogas. Los destilados medios pasan por un proceso de desulfuración en el que se extrae el azufre y se convierten en gasóleos y queroseno.
El producto más pesado de la destilación atmosférica sirve posteriormente de alimentación a las plantas de destilación a vacío para continuar obteniendo productos útiles para el día a día.
En la destilación a vacío se procesan, bajo condiciones termodinámicas adecuadas, fracciones pesadas del crudo. De esta forma se obtienen productos de mayor valor que pueden alimentar a otras unidades. >
Los gasóleos resultantes de la Unidad de Vacío (GOV) pasan a las unidades de conversión donde se convierten productos pesados en ligeros, más valiosos y demandados, como gasóleo y queroseno.
Estas unidades disponen de una tecnología muy avanzada y transforman completamente el panorama de la refinería de Cartagena. Con ellas se puede procesar una amplia gama de crudos, mientras que antes solo se podían destilar crudos de alta calidad. Actualmente la capacidad de conversión en Cartagena es del 90%, cuando antes era del 0%.
Una de estas unidades es la planta de hydrocracking. Aquí se mejora la calidad de los productos incorporando hidrógeno, y se elimina el azufre a los combustibles que luego se utilizan en los vehículos, evitando así que éstos lo emitan a la atmósfera.
Gracias a este proceso conseguimos productos con propiedades valiosas como combustibles de motor y aviación.
El otro producto resultante de la unidad de vacío, el fondo pesado, sirve de alimentación al coker. Esta unidad de proceso es la más grande de España en su categoría, con el tamaño de un edificio de 13 pisos y una capacidad de procesamiento de tres millones de toneladas al año.
Allí vuelven a transformarse los productos más pesados para obtener GLP, naftas y gasóleos, que posteriormente también pasan por un proceso de desulfuración. El resto es coque, o carbón de petróleo, con una alta utilidad como combustible industrial. Con las nuevas instalaciones, Cartagena pasa de no producir nada de coque a obtener 1.200.000 toneladas al año.
Aquí se convierte el sulfuro de hidrógeno en azufre elemental mediante reacciones químicas y catalíticas. Después se solidifica, se muele y se almacena para la venta.
La tecnología de Repsol puede eliminar el 99,5% del azufre contenido en los productos, un 1% más de lo que exige la legislación española.
Las plantas auxiliares son indispensables para realizar el proceso de refino y para garantizar el correcto funcionamiento del complejo industrial. En Cartagena hay ocho, y entre ellas destacan la de cogeneración y la de tratamiento de aguas residuales.
La primera aporta energía a las demás plantas gracias al gas natural. La segunda permite reutilizar una mayor cantidad de agua, y devuelve a la red la que ya no se utiliza en condiciones óptimas.
Desde este lugar se controla el funcionamiento de toda la refinería. Recibe miles de datos que se obtienen a través de un complejo sistema de recopilación de información sobre la actividad en la planta.
Es la caja negra del complejo industrial de Cartagena, donde decenas de ordenadores registran todos los procesos y modos de actuar de los equipos y especialistas. Son edificios construidos con un alto nivel de seguridad y protección a prueba de incidentes, que garantiza la continuidad de las operaciones en cualquier escenario.
En esta planta se fabrican bases de aceites lubricantes que abastecen al mercado doméstico y de exportación. El producto sale de tal forma que los fabricantes solamente tienen que añadir sus aditivos y envasar el resultado final.
También se obtienen aquí otros productos de alto valor añadido, como parafinas, asfaltos, betunes o materias primas para la fabricación de neumáticos.
Este tipo de paradas de mantenimiento están programadas y se rigen por un calendario plurianual. Se irán repitiendo de forma periódica para la revisión y mantenimiento de las unidades de la planta.
Las paradas programadas son actuaciones de mantenimiento preventivo y correctivo, en las cuales intervienen los equipos de las plantas industriales para asegurar su nuevo ciclo operacional proyectado. Después de una parada de estas características, la unidad afectada recupera plenamente sus condiciones originales para operar de forma segura y más eficiente, de acuerdo con los más altos estándares de seguridad, realizándose con la mayor optimización posible en tiempo y costes.
Tras el proyecto de ampliación, la refinería de Cartagena ha revisado su plan plurianual de paradas, adecuándolo a su nuevo esquema de producción, el cual supondrá programar y ejecutar una parada anual, con un alto volumen de trabajo, durante los próximos años para las áreas de Conversión y Lubricantes. Descubre la parada en cifras.